Process Improvement Methodologies
There are several different process improvement methodologies that companies can choose between. The right approach for your company can be based on a combination of your company’s needs, leadership matrix and individual preferences. Some leaders prefer Six Sigma, while others would prefer to use Lean, rapid improvements, total quality management (TQM) or theory of constraints — or a combination of these (such as Lean Six Sigma).
The most common process improvement methodologies are:
Rapid Improvement
Rapid Improvement is a technique for quickly implementing solutions when the problem is clearly defined and solutions are known.
Streamlined rapid improvement frameworks such as Kaizen or Just-Do-It are designed to be action-oriented and address readily apparent issues to drive value. They apply a simple tactical focus: to fix known problems with obvious quick fixes that are easy to implement and carry minimal risk.
Lean Process Improvement
Lean Process Improvement, or “Lean,” is a customer-centric methodology used to continuously improve processes through the elimination of waste. For example, if you’re improving your processes via a purely Lean lens, you will look to rapidly — yet methodically — remove the non-value-added steps within your process.
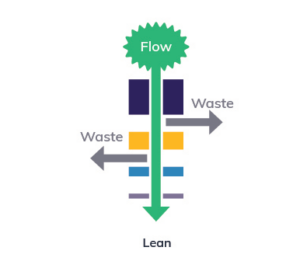
Lean is known as a methodology for the people, by the people. It forces you to evaluate each step within a process and ask yourself or your team, “Is this step in the process adding customer value?” If the answer is “no,” or if you’re uncertain, it is incumbent upon the team to look for ways to eliminate that step or mitigate the time it takes to perform that step in the process.
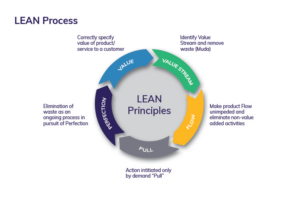
Lean thinking should be standard, not an afterthought in the business improvement process.
Six Sigma
Statistics and data-driven, Six Sigma seeks to improve the quality output of a process. This methodology focuses on identifying and removing the causes of defects (errors) and minimizing variability.
In the Six Sigma methodology, all processes can be defined, measured, analyzed, improved and controlled to drive repeatable and predictable performance. Each project follows a defined sequence of steps and has expertized value targets, including:
- Reduce process cycle time
- Increase customer satisfaction
- Reduce pollution, reduce costs
- Increase profits
A Six Sigma process is one in which 99.99966% of all opportunities are statistically expected to be free of defects.
Employing Six Sigma involves developing a group of people within the organization who are experts in quality management skills and methods using empirical, statistical techniques.
Lean Six Sigma
Organizations often combine Lean and Six Sigma to optimize capacity, reduce cycle time, and eliminate variability in all processes. Add in cross-analysis and communication and you have a powerful combination in problem resolution.
Let’s take a look at how communication and cross-analysis can decrease unintentional negative impacts on customer or employee experience. For example, if a restaurant hoping to improve
their customer experience simply improved one step of the process, they would have only gone so far. One improvement likely would not have positively impacted the customer experience long term.
But what if they decide to add the ability for a customer to place an order on a website? They’d need to investigate if they have solved consequential potential issues. If they look at every aspect of that process, from the ordering experience to the preparation and pick up of the order, they’d see the bigger picture of issues that are impacting customer experience, like delays and confusion in the pickup process.
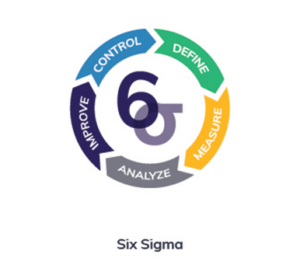
By looking at the entire process — considering each possible hand-off and touchpoint — and seeking improvement, the restaurant can transform from a highly dissatisfying customer experience to delighting visitors with fast, friendly curbside delivery of their meals with minimal wait times.
Six Sigma: DMAIC
You can — and should — take several steps to improve a process. DMAIC is an acronym that outlines the five phases of the methodology within Six Sigma tools. The goal of DMAIC is to reduce variability within your processes.
DMAIC stands for:
- Define the opportunity or problem, along with project goals.
- Measure the impact and process performance of an issue or process you are trying to resolve.
- Analyze the situation using tools like root cause analysis to determine what is causing defects or poor performance.
- Improve the process by addressing root causes identified through the analysis step.
- Control the new process to sustain your results.
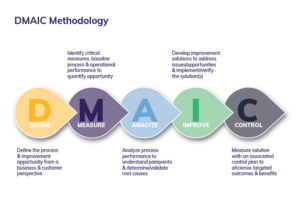
A common mistake made during the DMAIC process is skipping the first three steps and going right into an improvement mindset. It’s easy to catch yourself saying, “I know exactly what’s wrong. If we do this, we will fix our problem.”
While this type of thinking may help identify a quick “solution,” it will not actually resolve the problem or improve the process long term. Taking time with each phase is critical to sustaining success. Six Sigma advocates will ensure your company reviews a solid data set during a project’s analysis phase and that those responsible for decision-making don’t jump to conclusions too quickly.
There are many critical aspects of improving a process. Still, companies often overlook determining how the process change might affect other departments — whether upstream or downstream from a process change. You’ll want to ensure you’re communicating the process change to all key stakeholders who will be impacted within your business.
TQM (Total Quality Management)
TQM, or total quality management, centers on long-term success through customer satisfaction. This methodology highlights the steps, “Plan, Do, Check, Act.”
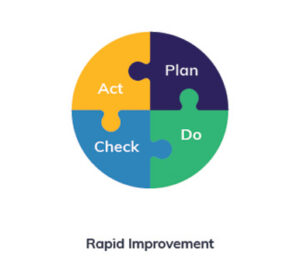
There are eight principles in TQM:
- Customer-focused
- Total employee involvement
- Process centered
- Integrated System
- A strategic and systematic approach
- Continual improvement
- Fact-based decision making
- Communications
As a management system, TQM is a continuous improvement approach that is based on the idea that every team member is dedicated to and maintains high work standards across a company’s operations.
Theory of Constraints
The Theory of Constraints (TOC) model focuses on finding the process bottleneck standing in the way of reaching an organizational goal, and then improving that process until it is eliminated or superseded by another limiting factor. The improvement process is repeated until throughput goals are achieved.
Because the Theory of Constraints is centered on maintaining an efficient workflow and continuous improvement, this methodology is frequently compared to Lean. Also, like Lean, the overall objective is to increase profit through cost reduction.